World-renowned innovations in tailored insulation compounds to meet our customers’ needs.
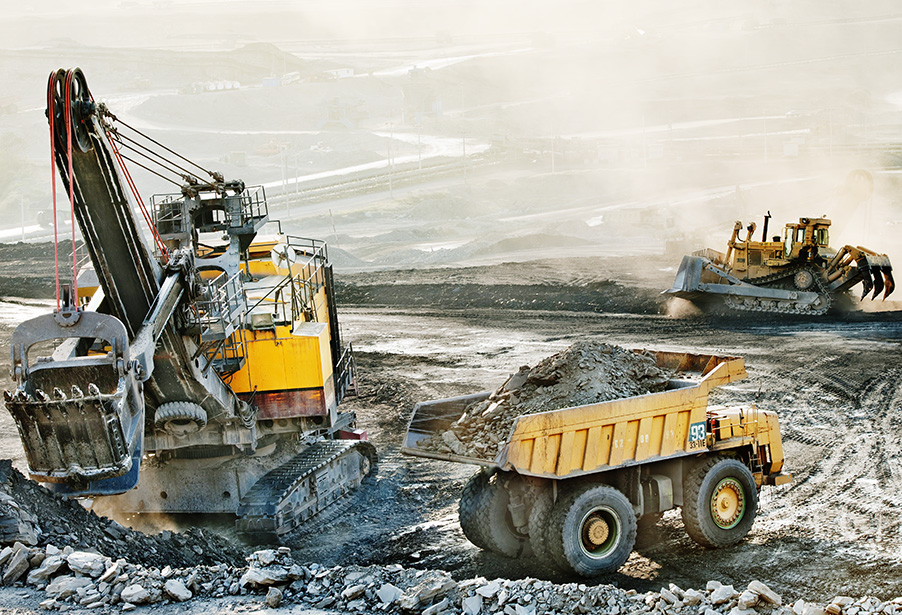
Our R&D commitment:
- Material innovation
- Superior resilience
- High value solutions
Research & development
Our research and development department has a global reputation as a leader in developing innovative insulating compounds to solve problems in wire and cable applications in harsh conditions.
Our R&D team’s focus is on delivering full satisfaction and cost-effective, cutting-edge solutions. We have an active and innovative team of polymer scientists committed to developing, through careful research, testing and trial and error, state-of-the-art insulation technologies to apply to wire and cable. These insulation compounds are cost effective alternatives to more expensive, and in some cases, lower performing insulations.
Irradiation technology
The laboratory is equipped to test and measure the following properties:
- High temperature rating
- Low temperature bend rating
- Predicting cable life via Arrhenius testing
- Voltage rating
- Chemical resistance
- Abrasion resistance
- High temperature cut-through resistance
- Fluid migration resistance
- Hot water resistance
- Oil swell
- Tensile strength
- Elongation properties
- Electrical insulation resistance
- Insulation capacitance
- Conductor resistance
- UV resistance
- Cable flexibility
- Flex life
R&D Success Story: EXRAD XLE 200
A large commercial vehicle manufacturer was experiencing failures with cables that were cracking in less than one year of use. The required operation life for the cables was 25,000 hours, or approximately five years. The cables were exposed to temperatures exceeding 170°C and the insulation cracked due to the high temperature exposure. Conventional cable insulations, such as Teflon® or silicone insulated cables, can withstand the higher temperatures, but these cable types have other problems. The Teflon® cables were too stiff and could not meet the bend radius requirements. The silicone cables were too susceptible to abrasion and cut through.
Our research and development team was asked if they could develop a solution to this problem; our team immediately got to work developing the XLE 200 cable. EXRAD XLE 200 is a highly flexible, abrasion and cut resistant insulation cable capable of withstanding temperature up to 225°C for 3,000 hours. We provided the customer with samples and an Arrhenius test report that proved the insulation would last over 50,000 hours in the operating conditions of the customer’s commercial vehicles. This product is now in production and is being used on many other platforms for other customers.
R&D Success Story: EXAR 150A
EIS is a partner distributor that sells components for the electric motor industry; Champlain Cable sold two motor lead wires to EIS. EXAR 150A is a well-known lead wire that has been used in the electric motor market for over 30 years. It has properties that help motor manufactures reduce scrap and rework. EXAR 150A is a great motor lead wire, but it is not as flexible as rubber insulated lead wire. Our R&D team developed EXAR SFX which is nearly as flexible as rubber, but does not have the excellent oil resistance properties of EXAR 150A. We then developed EXAR SFX-OR, a cable that combines the flexibility of EXAR SFX with the oil resistant properties of EXAR 150A. The SFX-OR insulation helps EIS to reduce inventory by stocking one EXAR product rather than two.