We are responsible for the successful future of Champlain Cable. Continuously improving our methods to be good citizens for our community, employees, shareholders and environment.
As a core value of our business, we strive to keep sustainability at the heart of what we do. From the resources we use to the products we make, we work hard to come up with creative solutions that are good for business and the environment.
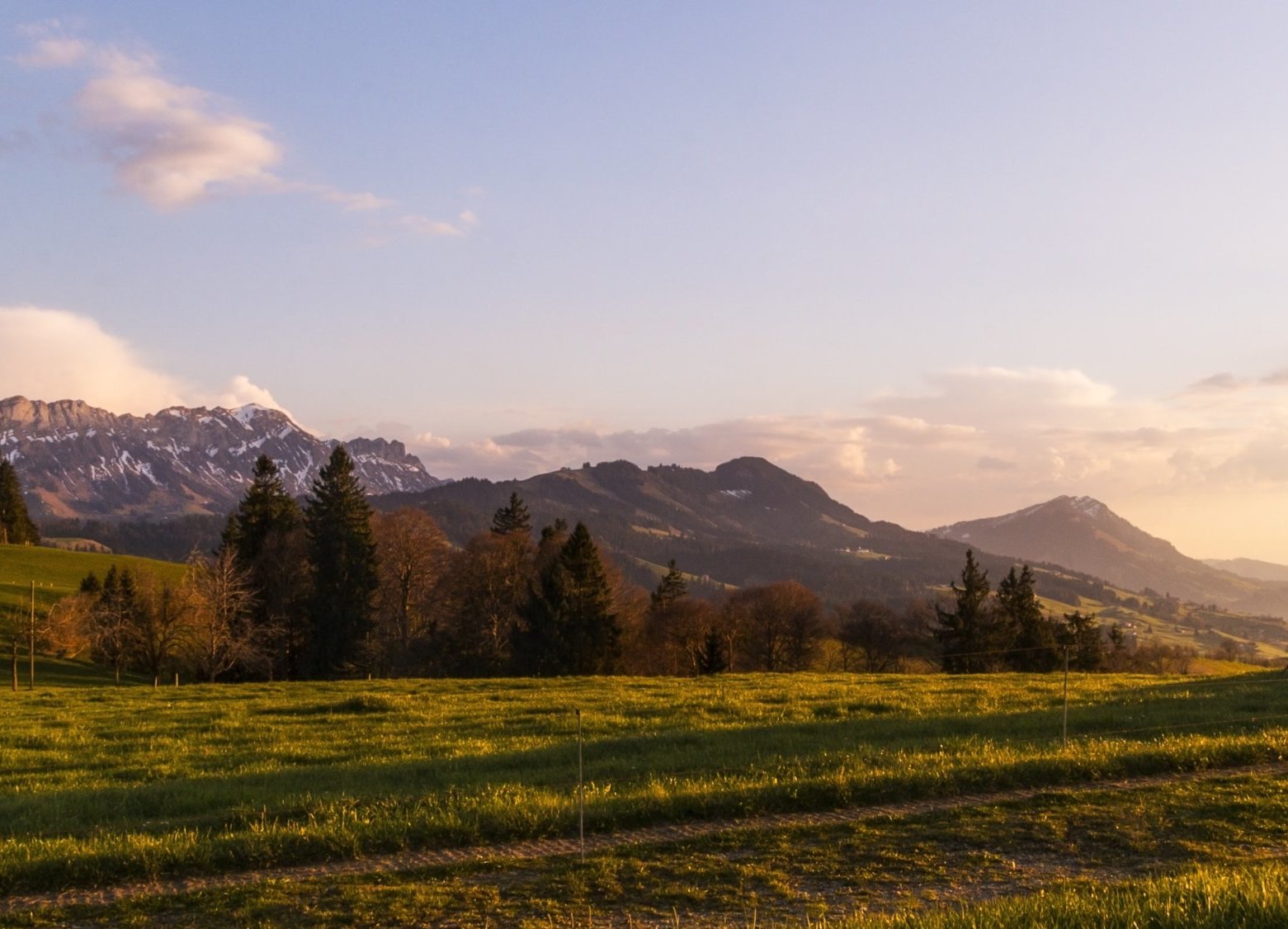
ISO 14001 – Certified Environmental Management System
Champlain Cable is proud to be certified to the ISO 14001:2015 standard for environmental management systems at our Colchester, Vermont facility. Our environmental management system (EMS) provides a structured approach for managing and reducing our environmental impacts. Below are a few highlights of our system:
Environmental Policy
Champlain Cable Corporation strives to ensure exceptional environmental performance in all its business operations.
Our primary aims include:
- Protection of the environment, including pollution prevention;
- continual improvement to enhance environmental performance; and
- fulfillment of all company environmental compliance obligations.
All employees have responsibility for policy implementation by participating and contributing to its success through their actions and suggestions.
Environmental Aspects
Resource Consumption
Waste Generation
Raw Material Usage
Here's just a few of our environmental initiatives
Process Scrap
Process Scrap
Although we make every effort to reduce the amount of scrap that we generate, we are still left with some manner of scrap material in the form of bare and insulated wire. When we can’t reuse these materials in our process, we partner with a scrap metal recycler and insulated wire processor to give these materials a second chance. All of our copper wire, whether its bare or insulated, is extracted by the recycler and sent back to a copper smelter where it can be melted down and reused to make new products.
Energy Efficient Pumps and Motors
Energy Efficient Pumps and Motors
For the last several years, our maintenance team has been working to replace our machine motors and pumps with newer, more efficient models. These new units utilize variable frequency drives (VFD). Compared to a traditional motor or pump that maintains a constant speed or flow, the VFD helps regulate the amount of power going to the device so that it can operate much more efficiently. These efficiencies across dozens of pieces of equipment results in significant energy savings.
Pallet Recycling
Pallet Recycling
Wood pallets are the backbone for stacking, storing, and transporting our raw materials and finished goods. Pallets are used and reused in our process as much as possible. What we don’t use is set aside and made available to a variety of third party businesses and individuals. This helps reduce unnecessary waste and extend the life of these useful materials.
Smart Thermostats
Smart Thermostats
Although Vermont is best known for its cold winters and high heating bills, the summers also mean heat, humidity, and air conditioning. In an effort to be more strategic with our heating and cooling, Champlain Cable has installed smart thermostats in our office areas and meeting rooms. This ensures that our employees are comfortable when they’re here, while also avoiding heating or cooling an empty room.
Case Study: Closed Loop Contact Cooling
During our extrusion process, the insulated wire passes through a series of water troughs to slowly cool the insulation. As a result, Champlain Cable was consuming millions of gallons of water each month. Beginning in 2000, we began the process of converting all our contact cooling to a closed loop system. This system allows us to reuse and recirculate the same water in our process as opposed to constantly refilling.
As a direct result of this effort, we saw a massive reduction in water usage.
Case Study: LED Lighting and Sensors
In 2017, Champlain Cable embarked on a massive LED light upgrade for our Colchester facility, replacing hundreds of existing fluorescent bulbs for energy-efficient LED’s. Dimmers and occupancy sensors were also installed to further reduce energy usage.
This project reduced electricity usage by an estimated 474,000 KwH per year as well as carbon emissions by around 451,000 pounds per year.